The Landscape of Plastic Mold Manufacturing
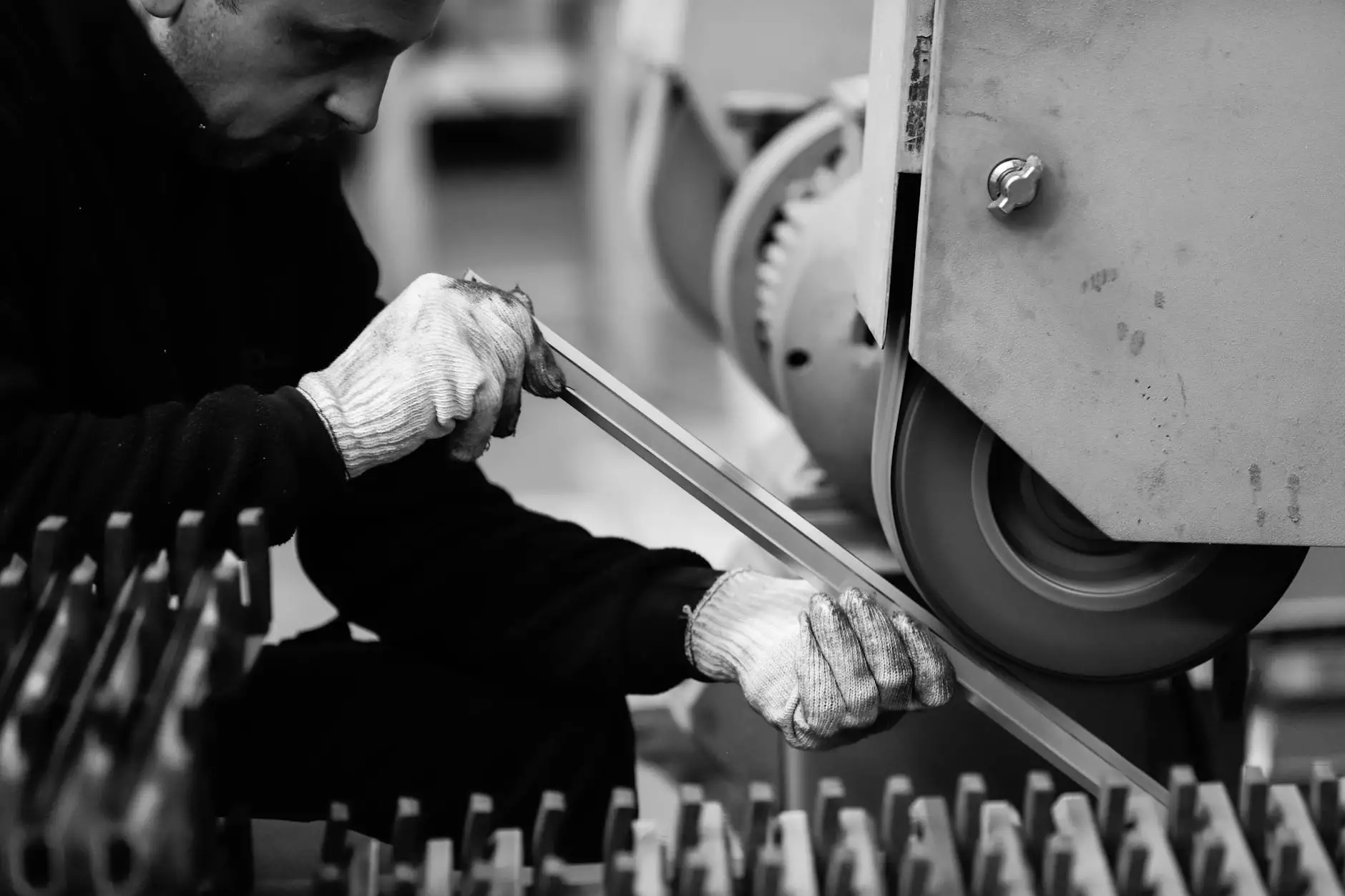
Plastic mold manufacturing has become a cornerstone of modern industrial processes, enabling the production of diverse products utilized in our everyday lives. From automotive components to consumer electronics, the precision and efficiency of molded plastics play a crucial role in how these items are crafted. This article delves into the depths of plastic mold manufacturing, exploring its processes, benefits, and future trends, while positioning DeepMould.net as a leader in this field.
Understanding the Basics of Plastic Mold Manufacturing
At its core, plastic mold manufacturing involves the process of creating plastic parts by injecting molten plastic into molds. These molds are crafted from materials that can withstand high temperatures and pressure, ensuring that they maintain their shape even under demanding conditions. The following are key steps in the process:
- Mold Design: The initial phase where engineers design the mold using CAD (Computer-Aided Design) software. Precision in design is critical as it dictates the final product's shape and features.
- Mold Fabrication: Once the design is approved, manufacturers create the mold using CNC (Computer Numerical Control) machines that ensure high accuracy.
- Material Selection: Choosing the right type of plastic is vital. Common options include ABS, Polycarbonate, and Polypropylene, each with unique properties suited for different applications.
- Injection Molding: In this phase, plastic pellets are heated until they melt and are then injected into the mold. After cooling, the mold is opened, and the finished product is ejected.
- Finishing Processes: The final parts might undergo additional finishing steps such as trimming, painting, or assembling to meet the product specifications.
The Benefits of Choosing Plastic Mold Manufacturing
Opting for plastic mold manufacturing comes with a myriad of advantages, making it the preferred choice for producers across various industries.
- Cost Efficiency: Once the initial mold is created, the cost per unit is significantly lower compared to other manufacturing methods, especially for large production runs.
- High Precision: Injection molding allows for tight tolerances and complex geometries, ensuring higher quality products that meet stringent standards.
- Material Versatility: A wide range of plastics can be used, allowing manufacturers to choose materials that offer the desired properties such as flexibility, durability, or heat resistance.
- Scalability: The process is highly scalable, suitable for both small batches and large-scale production without significant adjustments to the machinery.
- Eco-Friendly Options: Innovations in biodegradable plastics and recycling processes enhance the sustainability of plastic mold manufacturing, making it a responsible choice for manufacturers concerned about their environmental footprint.
Applications of Plastic Mold Manufacturing
The applications of plastic mold manufacturing are immense and span numerous industries:
1. Automotive Industry
In the automotive sector, plastic parts are vital for reducing weight and improving fuel efficiency. Components such as dashboard panels, bumpers, and interior trim are commonly produced through injection molding.
2. Consumer Electronics
Plastic mold manufacturing is critical in producing durable and attractive housings for electronic devices such as smartphones, tablets, and laptops. The precision of the mold ensures a perfect fit for internal components.
3. Medical Devices
From syringes to complex surgical instruments, the medical field relies heavily on plastic molds for creating components that meet stringent regulatory standards for safety and efficacy.
4. Household Products
Common household items, including kitchenware, storage containers, and toiletries, are predominantly manufactured using plastic mold techniques due to their cost-effectiveness and efficiency.
5. Industrial Applications
Many industrial tools and parts, such as piping systems, connectors, and machinery components, also utilize plastic mold manufacturing for their durability and resistance to corrosion.
Modern Innovations in Plastic Mold Manufacturing
The landscape of plastic mold manufacturing is evolving rapidly, integrating modern technologies and methodologies to improve efficiency and quality.
1. 3D Printing for Prototyping
3D printing technology has transformed the prototyping process, allowing for rapid development of molds before committing to the expensive fabrication of traditional molds. This not only saves time but also provides flexibility in design adjustments.
2. Automation and Robotics
With the integration of automation, the injection molding process has become faster and more reliable. Robotic arms can handle the repetitive tasks of part handling, assembly, and quality control, reducing labor costs and human error.
3. Advanced Materials
The development of new plastic materials, such as high-performance polymers and composites, allows manufacturers to create parts that can withstand more extreme conditions, thereby broadening the scope of applications.
4. Industry 4.0 Integration
The principles of Industry 4.0 are being applied to plastic mold manufacturing, incorporating IoT technologies for real-time monitoring and data collection to streamline operations and enhance decision-making.
Challenges Faced in Plastic Mold Manufacturing
While plastic mold manufacturing offers numerous advantages, industry players also face specific challenges that need addressing for sustained success.
- Initial Costs: The upfront investment for creating high-quality molds can be significant, which might deter smaller companies from entering the market.
- Design Complexity: As products become more complex, designing molds to accommodate intricate features can be challenging and require specialized expertise.
- Environmental Regulations: Compliance with environmental regulations concerning plastic production and disposal is becoming increasingly stringent, necessitating ongoing adaptation by manufacturers.
- Market Competition: The landscape is highly competitive, with many companies vying for the same contracts, pushing the need for continuous innovation and differentiation.
Quality Assurance in Plastic Mold Manufacturing
Quality assurance is paramount in plastic mold manufacturing. A product's success hinges on its reliability and safety, necessitating rigorous testing and validation processes.
1. Material Testing
Before production, materials undergo thorough testing to ensure they meet required specifications for strength, flexibility, and thermal resistance.
2. Mold Inspection
Inspecting molds before they are put into production helps identify potential issues that can lead to defects, ensuring high-quality output from the start.
3. In-Process Monitoring
Using advanced monitoring systems during the molding process allows manufacturers to track critical parameters, ensuring consistency and quality throughout production.
4. Final Product Quality Checks
After the parts are produced, they undergo final inspections, including dimensional checks and functional testing, to verify they meet all specifications and tolerances.
The Future of Plastic Mold Manufacturing
Looking forward, the landscape of plastic mold manufacturing is set for transformative changes driven by technology, sustainability, and market demand. Key trends anticipated include:
- Increased Use of Sustainable Materials: As the industry shifts towards eco-friendliness, we can expect a rise in the use of biodegradable and recycled plastics.
- Advanced Simulation Software: The implementation of more sophisticated software for mold design and process simulation will enhance accuracy and reduce timeframes.
- Customization and On-Demand Production: The demand for customized products will lead to greater flexibility in production runs, allowing manufacturers to respond quickly to market changes.
- Emergence of Hybrid Manufacturing Processes: Combining traditional molding techniques with additive manufacturing will result in new possibilities for product innovation.
Conclusion
The world of plastic mold manufacturing is dynamic and continually evolving, presenting vast opportunities for efficiency, innovation, and custom production in multiple industries. With the advantages it offers, from cost-saving benefits to scalability, companies like DeepMould.net are well-positioned to lead this charge. Embracing modern technologies and a commitment to quality will not only help overcome challenges but also ensure the sustained growth of the industry. As we look ahead, it is clear that plastic mold manufacturing will remain an integral part of global manufacturing, driving progress and innovation for years to come.